Common Welding Wire Problems And How To Fix Them
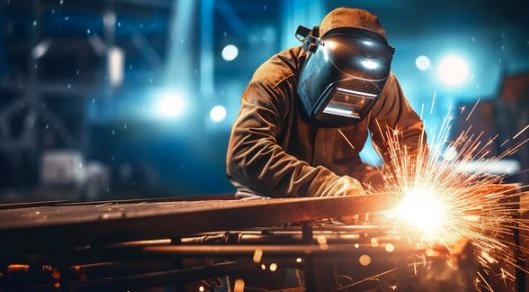
Introduction
Welding is a basic process in a plethora of industries, therefore the quality of the weld heavily depends upon the welding wires. As a seasoned professional or just a hobbyist, trouble with your welding wire is a nuisance, and can also lead to real problems with your results. Join us as who discuss some of the welding wire problems you may run into and offer some practical solutions to keep you welding.
Find more information about welding wire and welding techniques at UDO website – https://www.udo.co.th/
Common Welding Wire Problems
- Wire Feed Issues
These are just a few of the most common problems people have with welding wire, and more often than not, they are related to a feed mechanism in the wire. A kinked-in-the-gun, or tangled wire at the feed tube may result in irregular welds, or significantly worse, break the wire. A worn drive roller, unaligned liner or incorrect tension can all cause this problem.
Possible Solution: Check drive rollers and replace them if they are worn. Flush or fix kinks/cuttings of the liners (Has a Zip-in liner Turn On and Off setting) By properly maintaining and tuning the wire feed system you can save yourself many issues related to feeding.
- Porosity
Porosity is a welding defect in which small holes or cavities appear on the surface or inside of the weld bead. There are a number of reasons this issue may occur, such as contaminants present in the welding wire, inadequate gas shielding, or bad welding practices.
Fix: Make sure the welding wire is not damp, oiled, or has some other debris on it. Leak, or unstable flow rate in gas shielding system. Finally, to help prevent further pinhole creation, modify your welding settings (travel speed, wire feed rate, etc.) to reduce porosity.
- Spatter
Spatter – Molten metal particles that spray around the weld and solidify, forming irregular shapes that are difficult to remove (and generally look unsightly). If your spatter is out of control, possible reasons are: using off parameters or an off distance of wire stick-out, or contaminated wire.
Solution: Simply adjust your welding parameters like voltage, wire feed rate to more closely match the welding parameters of the material to be welded. Keep proper wire stick-out length and protect the wire from contaminants. The right welding technique and following basic welding basics can lessen spatter by a large margin.
- Wire Burn-Back:
Wire burn-back is where the welding wire burns back up into the contact tip or liner and obstructs the flow of wireThrough which disrupts the smooth wire feed. This issue is usually the result of improper heat input, too large of contact tip, or poor gas shield coverage.
Solution: Change the contact tip to match the diameter of the welding wire you are using. Flow the shield coverage gas Also, change your welding parameters to reduce heat input and avoid wire burn-back.
Summary
Welding wire is one of the key elements in the welding operation process, and how to solve common problems associated with wire feed issues, porosity, spatter, and wire burn-back is necessary to create high quality welds. This blog highlighted various solutions that will help you in troubleshooting weld wire problems so you can continue your welding operations in a smooth and flawless manner. Through simple maintenance, setting the welding wire correctly, and following best practices you should be able to avoid and solve these common dilemmas when it comes to working with your welding wire.