EXPLORING TIG WELDING: TECHNIQUES, APPLICATIONS, AND ADVANTAGES
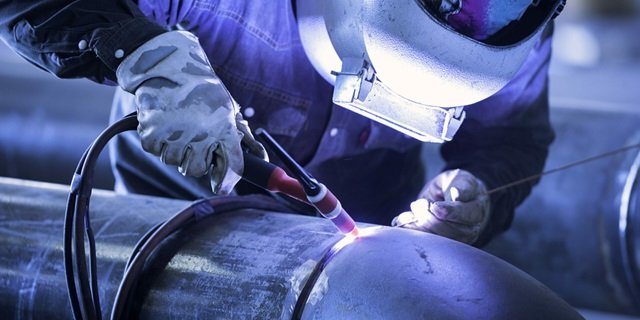
TIG welding is a precise and adaptable technique that can produce high-quality welds. It uses an inert gas, like argon, to shield the welding area from ambient contamination while joining metals with a non-consumable tungsten electrode. TIG welding’s primary selling features are its remarkable control and adaptability, which allow it to join assorted metals, including copper, aluminum, and stainless steel. Find out more about it below:
How It Works
Tungsten Inert Gas Welding employs a non-consumable tungsten electrode, which forms the welding arc with the workpiece. Tungsten inert gas, or “TIG” for short, is the non-reactive gas shielding the weld region from airborne contaminants and not affecting the welding procedure.
Shielding gases, such as argon, protect the torch electrode from oxygenation while simultaneously shielding the molten weld. The filler material might not be required for TIG welding.
Melting the groove together is another way to fuse the parts. If filler is needed, it is manually added to the molten weld rather than using a welding torch, as in MIG/MAG welding. As a result, a TIG welding torch has an entirely different structure than a MIG/MAG torch.
Several TIG welding techniques exist, including pulse TIG, AC TIG, and DC TIG, which use alternating and direct currents.
What is the distinction between MIG and TIG welding?
TIG welding differs from MIG welding in a few ways. While MIG welders employ a consumable electrode and a constantly supplied wire, TIG welders use a non-consumable tungsten electrode. TIG welding provides more control and precision and yields cleaner welds with less spatter, making it ideal for sensitive applications and thin materials.
Uses of TIG Welding
TIG (tungsten inert gas) welding primarily combines metals with extreme control and precision. Automobile, aerospace, and fabrication companies frequently use TIG welding. It offers exceptional weld quality with less distortion and is particularly well-suited for thin materials.
Pipe and pipeline welding are the two most significant uses of TIG welding. Nonetheless, it finds application in numerous sectors, including aviation, aerospace, and sheet metal, particularly in joining thin, unique materials like titanium.
Some examples of these applications at Micro Weld include the following:
- Fabrication: TIG welding joins non-ferrous metals such as copper, aluminum, and others for various fabrication operations.
- The automotive industry uses TIG welding to build engine components, gasoline tanks, and exhaust systems.
- Aerospace sector: Fuel lines, aluminum and titanium structural elements, and engine parts are among the airplane items that use TIG welding.
The Benefits of TIG Welding
TIG welding has the following benefits:
- It produces welds that are neat, precise, and visually pleasing.
- It can weld numerous metals like nickel, copper, aluminum, and stainless steel alloys.
- Precise heat control makes TIG welding possible for thin materials.
- The process results in less post-weld cleanup because it creates less spatter.
- TIG welding yields good fusion and solid and dependable welds.
THE BOTTOM LINE
TIG welding is a popular choice when precise, superior welds are needed. It is typically ideal for thin materials, delicate seams, and non-ferrous metals like brass, copper, and aluminum. TIG welding produces extremely minimal spatter and crisp, resulting in visually appealing welds.