How gear cutting tools manufacturers minimize material waste effectively?
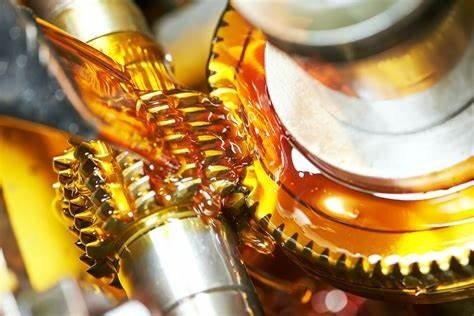
Gear machining is an essential component in many industries, such as the automotive, aerospace, and heavy equipment industries. The quality of the end product also depends on the right form of the manufacturing process to be used. It is not only the method that needs to be established but due to performance and safety issues, strict norms and guidelines have to be adhered to. The purpose of this article will be to provide an overview of gear machining, why it has become essential in manufacturing, and some of the methods that make up successful manufacturing. The gear cutting tools manufacturers industry, in general, is pursuing higher levels of production efficiency and enhanced product quality as well as environmental health.
Increased precision
Computer numerical control machines have been invented to minimize the use of handheld cutting tools such as chisels. While there is still useful information available on manual tool use, like pantographs, they are not as useful since they demand a lot of proficiency to be operated. Some CNC machines are planned using computerized design appliance to order activities. This precision carries over to fewer errors during production. It lowers the odds of being wasted because several pieces of material have to be cut to get a single perfect piece.
Effective chip management
In order to reduce the size of the chip formed and enhance chip evacuation, it is appropriate to fine-tune your working variables: the cutting speed, feed rate, and depth of cut. Storing chip accumulation also poses some forms of risks to safety. So, to avoid the above calamities, you need to seek proper chip management strategies that enhance the smooth operation of the firm. It is shaped like a single or several cylindrical tools, with cutting blades arranged around the circumference and chip flutes.
Gear generation
The machining process known as “gear generation” creates gears by continuously cutting material out of the gear blank. This method is based on the idea of concurrently rotating the cutting tool and the blank to create the gear tooth profile. Because it enables producers to produce large quantities of gear with reliable accuracy, gear generation is perfect for mass production. For spur gears, helical gears, and bevel gears—where exact tooth creation is crucial—this technique is particularly helpful.
Why choose the gear hob manufacturers?
Since its origin, gear hobbing has been transforming the manufacturing sector and remains one of the most economical and effective ways to produce high-quality gear. In this blog post, we shall go over some amazing advantages that gear hob manufacturers in India offer. As well as cutting gears, hobbing is always used to slice sprockets and splines. The adoption of CNC machining has greatly improved the efficiency of hobbing and gear cutting in general. Now, let us see how this technology aids in the production of gears. The process of machining gears with spiral or straight teeth is called gear hobbing. Worm gears, helical gears, and spur gears are all made using this method.